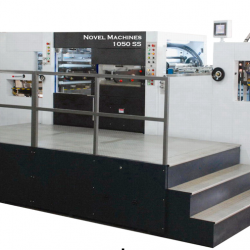
Automatic Die Cutting Machine
When it comes to postpress and finishing processes, quality is a crucial factor. Our Automatic Die Cutting machines work precisely and efficiently.
Machine features
Feeder Part
- A four-suction/four feed powerful mechanism which enables quick delivery via stable and smooth paper feeding and of which the height and angle of the suction nozzle can be adjusted accordingly.
- An on-off preparing trolley that increases the efficiency in operating the machine.
- A slanting paper feeding worktable that makes the machine more suitable for transmission and positioning of thin paper in high-speed motion.
- A nonstop unit as a lift platform for paper transmission.
- A double-expansion control unit.
- A side-positioning pull-push lateral-arrangement unit that can be switched easily for different types of paper quality.
- An imported quality blowing/suction double-purpose vacuum pump.
- A unit that reduces the speed before the system is switched to the desired gear and therefore facilitates the positioning of thin paper in high-speed motion.
- A paper transmission rubber hand wheel that can adjust the system in an interconnected manner and thereby increase the efficiency.
Die Cutting Part
- A worktable on which a toggle-link-type high-precision plane die driven by a worm wheel’s crank cuts downwards.
- A worktable on which a toggle-link-type high-precision plane die driven by a worm wheel’s crank cuts upwards.
- All machine elements in the heart of the machine (including the crankshafts, worms, worm wheels, and toggle link-type shaft) are made of imported high quality alloy steel.
- Two sets of die cutting steel plates with a hardness of HRC45-47 that are accurate and durable and can be locked while being aligning to one side.
- A pneumatic locking system for the plate frame of the die cutting part.
- Imported pneumatic clutch and brake.
- An electric digital display unit for pressure indication that facilitates ease of precise operation in adjusting the die cutting platform’s elevation and its pressure in tons.
- A front-mounted positioning flip-flop plate that enables four-point fine-tuning to adapt to precision positioning under different paper-related conditions.
- Advanced technologies adopted that together enable fore-and-aft fine-tuned compensation when positioning is realized by a single tooth bar, thereby guaranteeing the precision requirements for product processing.
- A drive mechanism that employs state-of-the-art technologies by integrating chain bars composed of multiple parallel cams (including imported cutter and torsion clutch).
- High precision imported drive chain for driving of paper clamping tooth bars.
- Seven imported paper clamping tooth bars, each containing ten tooth pieces of quality steel and their matching counterparts.
- Paper inlet and outlet, each equipped with electric eyes for detection of the correct positioning of the passing paper sheet.
- Electric eyes coupled with a large-capacity human-machine interface LCD, which together monitor the entire process and provide detailed information on how to troubleshoot an outstanding problem.
- A 1.5-kW cooled circulating unit adopted for supply of oil to the forced lubrication system in the heart of the machine, equipped with an oil pressure display unit and an alarm unit for insufficient oil and air pressure.
- A unit for leveling paper sheets before they are fed in for die cutting.
Waste Removal part
- A triple-interlocked-piece waste removal unit that enables effective removal of various types of waste through harmonious and precise operation.
- A double-layer drawer-type structure that contains upper and lower dies and therefore enables quick disassembly and calibration of waste removal tools.
- An intermediate waste removal plate frame that enables convenient adjustments.
- An upper frame that uses an electrically-controlled lifting unit.
- A standard waste removal impact pin and an elastic push rod that together completes perfect ‘impact-pull’ operations.
Paper Reclamation part
- A fully-automatic primary and secondary paper reclamation tables that guarantee ease of operation and greatly increased production efficiency, with a curtain cloth adopted on the secondary table for realization of up-and-down switchovers. This configuration can substantially facilitate operation and makes it easier to process products manufactured with multiple spliced plates.
- An inset counter.
- A buffer unit for the tension wheel of the tooth bar drive chain.
- A stepwise-adjustable hair brush and a unit for leveling paper sheets by blowing, which together stabilize finished products transported to the paper reclamation part.
- An automatic chain oil loading unit for lubrication of the master chain.
Electric Control part
A PLC that can control the operation of the entire machine and its temperature failure monitoring system.
Electric components and electric wiring in compliance with advanced standards commonly adopted by U.S.A. and European countries (CE standards).
Machine Specifications
Model |
1050SS |
Maximum paper dimensions | 1050 × 750 mm |
Minimum paper dimensions | 400 × 360 mm |
Maximum die cutting range | 1040 × 720 mm |
Inside dimensions of the plate frame | 1080 × 745 mm |
Die cutting steel plate’s dimensions | 1080 × 736 mm |
Applicable paper range | 80~600g/m2 paper & board |
Thickness for corrugated paperboard | ≤ 4mm |
Minimum width of wasted edge | 9.5 mm (depending on how the product is arranged, the paper in use, and how the machine is operated) |
Maximum machine speed | 7500 RPH (depending on how the product is arranged the paper in use, and how the machine is operated) |
Maximum pressure cutting force | 300 tons |
Total power consumption | 20 kW |
Compressed air pump | 0.36 m3/min as the rate of compressed air displacement (cubic meter per minute) |
Requirements for the power supply | 380V, three phases, 50 Hz (a transformer of 25KWA in capacity shall be provided by the user if the local voltage does not comply with the corresponding requirement) |
Net weight | 15 tons |
Outside dimensions of the complete machine |
7380 × 4210 × 2120 mm (L x W x H) |
Related Products
Automatic Die Cutting Machine
When it comes to postpress and finishing processes, quality is a crucial factor. Our Automatic Die Cutting machines work precisely and efficiently.
Creasing and Die Cutting Machine
RQ serial die cutting & creasing machines are special equipments for die cutting and creasing a wide range of materials, such as cardboard, corrugated board, plastic and leather. They are applicable to the fields of printing, packaging, decoration and plastic industries.
Automatic Foil Stamping and Die cutting Machine
The TL780 Automatic Foil Stamping and Die Cutting Machine is designed for the Hot Stamping, Die Cutting, Pressing Convex and Creasing etc techniques, it’s suitable for paper, cardboard, plastic film and so on. It can finish feeding, die cutting, collecting work cycle automatically.
Hot Stamping and Die cutting Machine
TYMB Serial computerized Hot stamping and Die cutting Machines are new generation products with high precision and marked effect. They are used for hot stamping all kinds of colored aluminum foil and embossing upon pictures, advertisement samples, trade mark covers of books, season greeting cards packaging cartons, and high grade decoration and printing materials.
Paper Embossing Machine (Sheet Fed)
It's widely used in embossing many kinds of paper, such as wall calendars, desk calendars, covers of books, lucky envelopes, invitation cards, congratulatory cards, packing paper-boxes and etc. Such a technology can make the products more beautiful and more exquisite.
Paper Embossing Machine Large Format (Sheet Fed)
It's widely used in embossing many kinds of paper, such as wall calendars, desk calendars, covers of books, lucky envelopes, invitation cards, congratulatory cards, packing paper-boxes and etc. Such a technology can make the products more beautiful and more exquisite.
Paper Embossing Machine (Roll Feed)
This machine is suitable for surface embossing and knurling processing of rolling paper, film, aluminizing film, aluminum foil, etc. It is an ideal machine for enhancing the aesthetic feeling of the products and decorative effect.